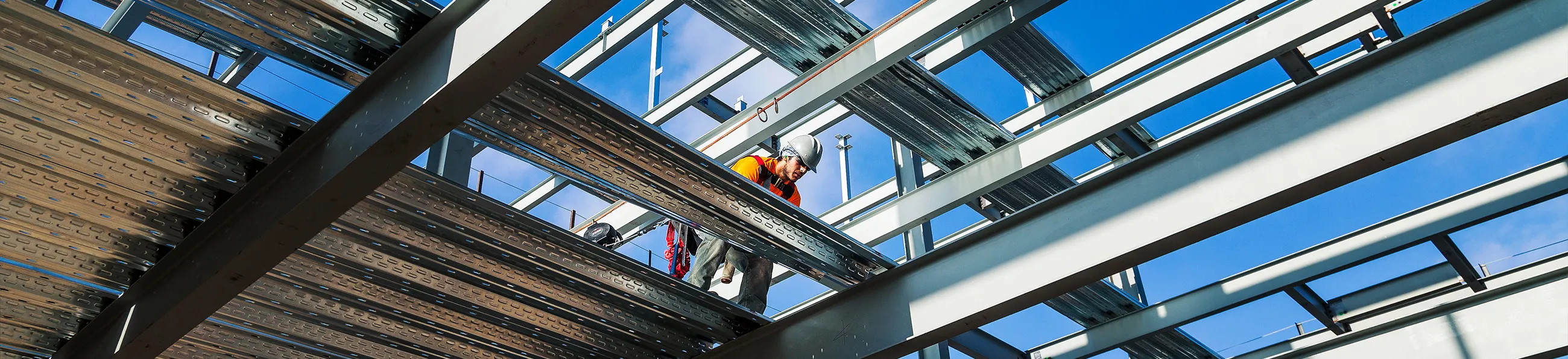
Futuristic $11 Million Headquarters Combats ‘Earthquake Country’
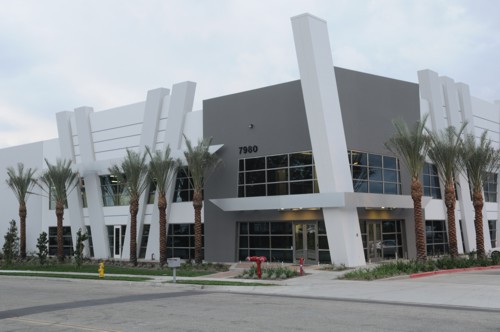
FONTANA, CA — A futuristic, $11 million corporate headquarters for Door Components, Inc. whose intentionally skewed “Leaning Tower of Pisa” façade at once displays the company’s cutting edge products while advancing seismic stability and energy efficiency, has opened in Fontana, CA, announces Oltmans Construction Co., the project’s general contractor.
Bob Briggs, president of privately-held Door Components, Inc., said his company will complete occupancy of its new headquarters this month (October). The facility, which consolidates two company sites in Rancho Cucamonga, is strategically located on a five-acre parcel of land at 7980 Redwood Ave. just east of Interstate 15 and north of Interstate 10. Approximately 160 people will be employed at the site. Established in 1981, Door Components, Inc. manufacturers hollow metal doors and frames along with stainless steel doors frames and window frames.
“We knew when we hired Oltmans we would get a quality, purpose-built facility. They exceeded my expectations; I couldn’t be happier. The building makes a statement about our company’s cutting edge,” said Briggs. “This is critical because we are a service company providing products customized to our clients needs. Bringing our entire operation under one roof also enhances this goal.”
Darin Lee, project manager for Whittier, CA-based Oltmans Construction Co., said the new Door Components headquarters is a concrete tilt-up, 93,183 square foot build-to-suit facility. He said the building features 13,000 square feet of two-story office space, 11 dock high loading positions and 30-feet of minimum warehouse clear height.
Byron Pinckert, a principal of HPA, Inc. of Irvine, architect for the building’s core and shell, said the Door Components building also establishes new ground in the use of the concrete tilt-up method. WLC of Rancho Cucamonga designed interior spaces.
“Concrete tilt-up construction has long been preferred for low-rise buildings in California. It’s cost effective, flexible, durable and fares well in periodic tremors of earthquake country. The shakes of earthquake country are the inspiration for a new twist on the venerable concrete tilt-up building reflected in the Door Components headquarters,” said Pinckert.
He explained that earthquakes shake buildings from side to side, forcing straight vertical structures into “imitations of the leaning tower of Pisa. “Teaming with Oltmans, we have made an allusion to those seismic forces by expressing skewed concrete tilt-up panels on the building’s facade. These panels appear to tilt much like the tower of Pisa, even while providing the same vertical stability of more conventional appearing design,” Pinckert said.
He said the skewed panels float adjacent to large expanses of glass that are framed with modified elements of Door Components’ standard product. Stainless steel door frames were adapted into the stainless steel glass curtain wall framework that sets off the tilted tilt-up panels.
“Juxtaposing the orthogonal glass system with the skewed panels leads the casual observer to wonder if this is a post-earthquake outcome,” Pinckert declared.
In addition to it singular design, Briggs added that his new headquarters accents a clean environment and the latest of industry equipment. He noted that a series of exhaust ducts in the warehouse exchange air five times per hour. Additionally, a new electrostatic spray paint system, cuts paint usage for finished products substantially while minimizing air pollutants, he said.
Moreover, the use of all stainless steel window frames and doors results in clean, durable, waterproof components, eliminating water leakage, rust, “and they last forever,” Briggs said.
Consideration for Door Components’ employees and efficiencies goes even further. To maximize forklift movement and safety, Briggs asked Oltmans to install diagonal brace frames above forklift level on three I-beams located down the middle of the building that further support the roof and bolster stability. Thirty yards of concrete lend added strength to I-beams five feet beneath the finished floor. “I know exactly where I’m going to stand in this building if there’s an earthquake,” Briggs said.