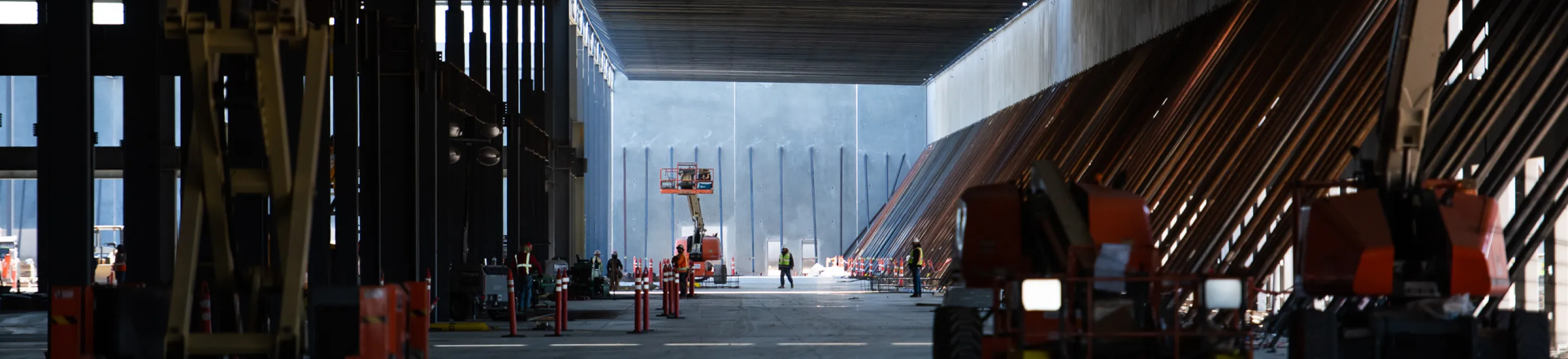
Toyota Logistics Services Vehicle Processing and Distribution Center (VDC)
Preconstruction and construction of a new Toyota Vehicle Processing and Distribution Center (VDC), to replace the existing VDC facility, within the same paved (144 acres less 16-acre reduction) lot.
Preconstruction and construction of a new Toyota Vehicle Processing and Distribution Center (VDC), to replace the existing VDC facility, within the same paved (144 acres less 16-acre reduction) lot. The new facility consists of a LEED Gold Certified 155,000 s.f. post production building, 5200 s.f. car wash and a 3,500 s.f. fuel island to replace multiple existing structures and consolidate the functions of the current VDC into a 21% smaller footprint. Part of the redevelopment also included a renewable energy fuel cell power plant that converts natural gas into water and electricity. The electricity is used to supply power to Toyota’s operations and the water is pumped to the car wash to be reused. The project creates a more efficient workflow, reduces vehicle movement and emissions, increases site safety, and updates the seismic security of the facility.
Preconstruction & Construction
Early engagement with the subcontracting community during preconstruction produced valuable constructability and feasibility inputs that were vetted by Oltmans’ preconstruction team and shared with Toyota and P2S, the project electrical engineer. During construction, the electrical subcontractor went on to assist with adding an electrical bus duct system throughout the production areas that provide Toyota’s operations team with maximum flexibility to modify their ever-changing processing requirements.
To comply with the Port of Long Beach’s security measures throughout construction, specialized employee screening was required through the Transportation Security Administration (TSA). All oversight personnel on the project were required to carry a Transportation Worker Identification Credential (TWIC) as required by the Maritime Transportation Security Act. Oltmans worked alongside the U.S. Coast Guard to ensure that proper compliance was met and that the expectation that random security checks would and did occur was communicated.
Underground Utilities
To prep the site for vertical construction, approximately 2-1/2 miles of underground utilities have been installed through a maze of undocumented oil lines, and 542 piles were driven, some as deep as 72 feet, into the ground.
One of the most challenging aspects of the underground scope has been overseeing and coordinating the processing of 3,000 cubic yards of contaminated dirt with the Port of Long Beach, navigating the complex, high-pressure sewage infrastructure. This involved four (4) new connections, three (3) of which were connected directly to a one-hundred-year-old sewer main located 15 feet below ground. No live pipes were disturbed during excavations.
To process the contaminated soil and groundwater, Oltmans teamed up with another contractor, who works directly with the port, to identify, remove, and export all contaminated material in compliance with AQMD regulations. To dry out and compact the trenches, water was pumped out 24/7, cleaned, and reused on-site for air quality control.
Another challenge posed was the oil pipelines of six (6) neighboring companies which ran underneath the project site, requiring coordination efforts each time the utilities crossed. This alone required a small army to ensure that where our underground utilities intersect with another company’s, we took the appropriate steps to verify and test, avoid, or cap and remove.
COVID-19
Initial COVID-19 shutdowns also affected the project’s ability to procure piles causing significant delays. To mitigate time lost, the team reconfigured the construction sequence to keep the project moving. As a union contractor, Oltmans Construction Co. controls a field force of over 300 carpenters, allowing us to exert strategic control of the schedule and meet manpower requirements despite a severely constrained labor force due to the pandemic. With the implementation of proper State and federal COVID guidelines the project team was able to avoid schedule disruptions and delivered the project on time.
Awards
- 2023 LABJ Commercial Real Estate Awards - Best Sustainable & Industrial Project of the Year
- 2023 NAIOP Gala Award - Sustainable Project of the Year
- 2023 ENR Awards - Best Airport/Transit